2019.8.23 – 画像追記更新 SMD、THD、THT、SMT、THM、SOIC、QFNのように、電子技術の術語は、電子工学の初心者に不必要な混乱をもたらす可能性があります。しかし、術語と技術は、思った以上はるかに簡単です。この記事では、これらの方法について簡単に紹介し、いつ、どのように使用するのかについて説明します。 SMは表面実装を表し、THならスルーホールを表します。これは、プリント基板上にコンポーネントを実装する2つの異なる方法を示します。SMまたはTHにおける、T、D、M、CまたはAは、技術、デバイス、取り付け、コンポーネントまたはアセンブリの略です。それらはかなり不真剣に使用される傾向があります。たとえば、SMDはSMAプロセスでSMCを使用するため、SMTで作られたものです。 SMとTHの両方のコンポーネントを使用するボードは、混合デバイスと呼ばれます。 SMTとスルーホール技術の違い from ssuser97ba8f 歴史:実装技術の発展 最初、すべての電子部品はスルーホール実装でした。スルーホール部品は金属リード線を持ち、これらのリード線は基板上のスルーホールを通します。次に、リードの端部は、反対側の面またははんだ面のパッドにはんだ付けされます。めっきされたスルホールを構成するドリル穴とパッドは基板表面に貴重なスペースを占め、多層基板には更になります。ドリル穴がすべての層のスペースを占めるからです。空間の制限が広がるために、表面実装技術が生まれ、さらに小型で持ち運び可能の電子機器の新しい時代を迎えました。 SMTとTHTの比較 SMTとスルーホール技術の違い from ssuser97ba8f 表面実装部品にはリード線がある場合とない場合がありますが、最も重要なのは部品本体と同じ面に直ちにプリント基板の表面に半田付けするように設計されています。したがって、ボードの両面を簡単に実装に取り付けることができ、めっきされたドリル穴は不要です。回路層の中のパターンを繋がるために、スルーホールを代わりに使用することができ、表面実装部品はめっきされたスルーホールと構造的には同じであるが、はるかに小さいです。更に、スルホールは基板の特定のレイヤのみに設計されます。したがって、めっきされたスルーホールがないなら、SMDデバイスに大幅なスペースを節約できます。 さらに、SMD部品のサイズと面積は、THD(DIP)部品と比べて、小型化できます。部品の端部を半田面とよく接続する為に、リード線は完全に省略することができます。したがって、抵抗、コンデンサ、インダクタ、さらにはLEDなどの多くの部品から、砂の粒のような(0201/0603パッケージ)のサイズまでSMDパッケージで発見されるようになりました。 しかし、小型化はSMDデバイスの信頼性に影響を与えます。このような基板の製造に必要なはんだ付けの複雑さおよび余分な精度のために、SMDアセンブリラインは一般に多数の欠陥があり、それになかなか修復できません。実装された基板はそんなに頑丈ではなく、取り扱いは十分ご注意を払わなければなりません。一方、基板の全体に幅が広がる大きなはんだ接合部があるので、TH部品で組み立てた基板は非常に頑丈です。この特性は、デバイスに強力な衝撃や振動を作用させる可能性があるので、軍事用途または産業用途に望ましいです。 コストもまた考慮すべき重要な事項です。SMD部品は一般にTHD部品より値段が安いが、SMT実装はTHT実装よりはるかに高価です。表面実装プロセスには、マウンタ(実装機)、リフロー炉など大型で高度な設備が必要で、もちろんカスタムスメタルマスクも必要です。一方、スルーホール実装プロセスには、いつかのはんだ、一つのはんだコテ、一対の頑丈な手が必要です。工具を使って、少数のSMD部品を手ではんだ付けすることは可能ですが、特に肉眼ではほとんど見えない多くの部品を取り扱っている場合には、これは面倒なプロセスです。したがって、高度な自動化とスピードを持つ大規模な製作ではSMTを使用し、手動による調整が必要な小規模のプロジェクトや試作ではTHTを取っておくのは必要になります。 まとめて 趣味の立場から見ると、ロープを習ってからスルーホール部品の利用は始まりました。SMTへの勉強は難しいように見えるかもしれないし、必要もなさそうです。 SMTの本当のメリットは、小型で複雑なデバイスを可能にし、大量生産をほぼ完全に自動化できることです。しかし、小規模生産と家庭用プロジェクトでは、SMTのコストとスピードのメリットはほとんどありません。したがって、必要な場合を除き、スルホールボードは一番です。 SMTの主なメリットは、SMD部品を使用して、部品の密度と体積を大幅に削減することができます。小型でコンパクトなデバイスの開発は、部品の形の要素を限界まで押し詰めてきました。。エレクトロニクスの現代では、THTは「ダサいもの」になっています。しかし、なくなるという早期予測にもかかわらず、スルーホールの技術と部品は依然として貴重であり、長期的に見ると、いつもあるようです。 #詳しく表面実装技術について知りたい方は、表面実装技術についてご覧下さい Seeed Studio Fusionは、小ロット、高品質のスルーホール実装とSMT実装サービスを手ごろな価格で提供しています。
詳しくへ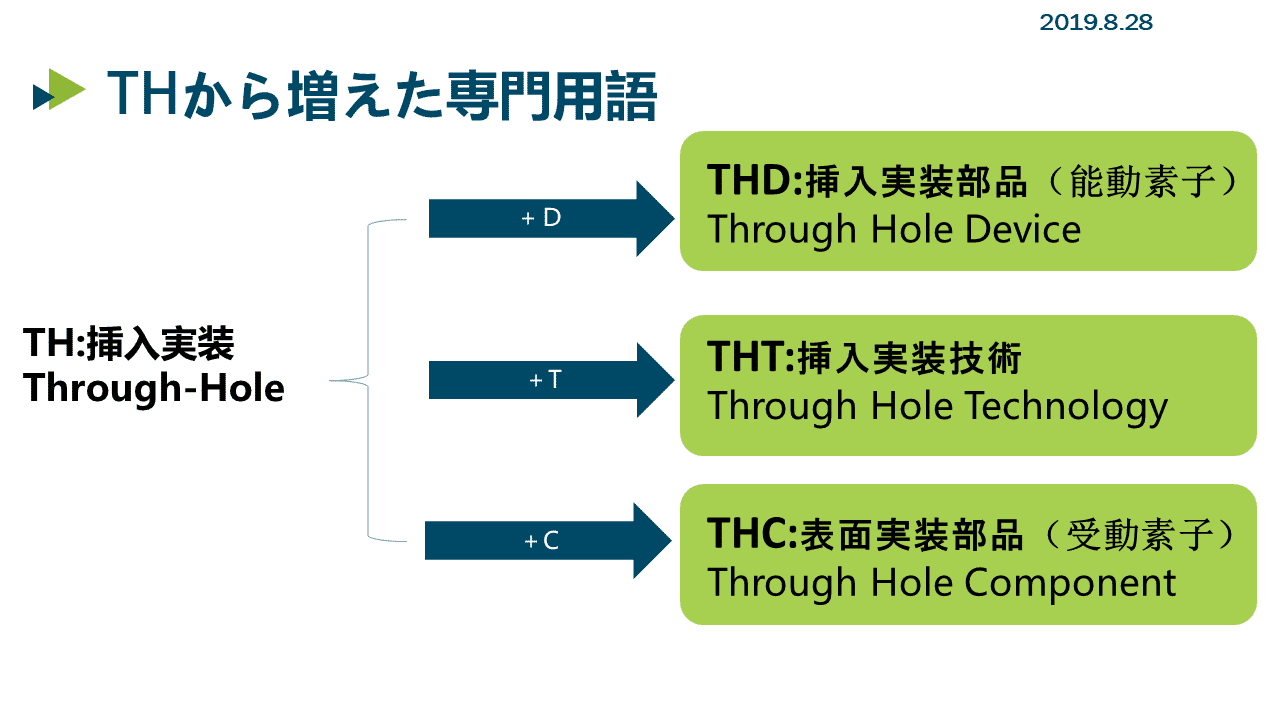